address:201, Factory 6, Longhui Industrial Park, Fuqiao 3rd District, Xinhe Community, Fuhai Street, Baoan District, Shenzhen china
How does the time-of-flight sensor PCB board work?
Have you heard of the time-of-flight sensor PCB circuit board that works in cameras and cell phones, but you don't know what it is and how it works? If yes, then you have come to the right place. Contrary to its name, the time-of-flight sensor PCB circuit board has nothing to do with measuring the flight of an aircraft. Instead, it's more of a sensor PCB that measures distance.
But if the concept of a time-of-flight sensor confuses you, don't worry. In this article, we'll explain when, how, and how a flight sensor circuit board works.What is a time-of-flight sensor PCB board?
A time-of-flight sensor PCB circuit board measures how long it takes to travel through a medium from one point to another. In other words, it measures the time it takes for an object to travel a certain distance.
Typically, a time-of-flight sensor PCB circuit board measures the elapsed time between when a wave pulse is generated and when it reflects off an object and returns to the sensor. Also, you can use different types of signals on the ToF sensor. But the more common signs you can find are lights and sounds.
ToF sensor PCB circuit board diagram
Source: Wikimedia Commons
Also, you can find the ToF sensor PCB circuit board in the time-of-flight camera. These devices use time-of-flight measurements to calculate the distance between the environment and the camera, and generate images from individually measured points.
A time-of-flight sensor is very powerful at distance sensing and ranging - mostly when it emits light rather than sound. Also, when you compare ToF with ultrasound, you will find that ToF provides faster readings, higher accuracy and greater measurement range. The best part is that it packs all of this functionality into its small, lightweight construction, and doesn't consume much power.
How does the time-of-flight sensor PCB board work?
As mentioned earlier, ToF sensors measure the distance between an object and the sensor. It uses tiny lasers that generate infrared light. Once it produces this light, it bounces off the surface of any object and moves back to the sensor.
Infrared lamp PCB circuit board
Infrared light
Likewise, ToF sensors measure the distance between an object and the sensor. So it's based on the time it takes for light to return to the sensor after it bounces off the object.
In fact, this is what happens on the surface.
Therefore, ToF sensors can use travel time to measure depth and distance in two ways. Additionally, you can run the above measurements using the phase shift of the timing pulse and AM wave.
So, let's take a closer look at these two measurement methods:
1. Use timing pulses
When the ToF sensor PCB circuit board measures distance using timed pulses, it first fires a laser at the target. After that, it uses a scanner to accurately measure the distance traveled.
Next, the sensor uses different wavelengths and laser return times to generate an accurate 3D digital representation of the target surface. After that, it creates a visual map of its features.
Additionally, ToF sensors use the following formula to provide accurate distance measurements:
(speed of light x flight time) / 2
2. Use the phase shift of the AM wave
In fact, ToF sensors can measure distance and depth by detecting the phase shift of reflected light through continuous waves.
When the sensor modulates the amplitude, it produces a sinusoidal light source.
Sine waveform
Sine waveform
Source: Researchgate
This form of known frequency enables the detector to measure the phase shift of the reflected light using the formula:
Phase shift formula
For this formula, c is the speed of light (3×108 m/s), λ is the wavelength (15m), and f is the frequency.
Furthermore, the sensor operates at the speed of light. So you can imagine the speed and precision with which sensors measure depth and distance.
However, the principle you choose does not matter. If you provide a light source to illuminate the scene, the sensor will measure the depth of the object. Additionally, the result creates a range map where each pixel shows the distance to a matching point on the object.
Benefits of Using a Time-of-Flight Sensor PCB
Below are some of the advantages of using time-of-flight sensors in distance measurement applications.
long distance
Since ToF sensors work with lasers, they can measure long distances and distances with great accuracy. For this reason, ToF sensors can detect near and far objects of different shapes and sizes - making them flexible.
Plus, its flexibility allows you to customize the optics of your system, so you only get the best performance and field of view you like.
cost effective
In terms of price, ToF sensors are more affordable than other 3D depth scanning technologies. However, its lower price does not affect its fast capture of 3D information.
Precise and fast measurement
The time-of-flight sensor PCB circuit board leaves other distance sensors, such as ultrasonic sensors, in the dust in terms of speed and accuracy. ToF sensors can detect objects quickly and are resistant to air pressure, temperature and humidity, making them ideal for indoor and outdoor use.
safe
You don't have to worry about laser damage to your eyes. Most ToF sensors have low-power infrared laser lights and use modulated pulses to drive them. Additionally, these sensors meet Class 1 laser safety standards and are safe to the human eye.
Limitations of ToF
As beneficial as ToF sensors are, several factors limit them. Here are some of those limitations:
multiple reflections
If you use a ToF sensor in concave shapes and corners, you may get unwanted reflections that alter the precision and accuracy of your measurements.
ambient light
Using the ToF camera in bright outdoor conditions such as sunlight can cause difficulties when measuring. Additionally, high-intensity sunlight can cause sensor pixels to saturate quickly. In other words, when light bounces off an object, the sensor won't be able to detect it.
Scattered light
If you have any bright surfaces near your ToF sensor, it may cause scattered light in the receiver. As a result, it creates multiple unwanted reflections that can obstruct the measurement.
Example of a time-of-flight sensor
Now that you are familiar with how ToF sensors work, let's take a look at some of the best sensors available for your project. These examples are suitable for a variety of applications, including automation and appliances.
Opene8008B-QVGA Time-of-Flight Sensor Evaluation Kit
Source: Wikimedia Commons
The Opene8008B-QVGA ToF Evaluation Kit is the perfect ToF camera with high resolution depth images. Additionally, you can get real-time visualization and recording of depth map data by connecting this camera to a PC.
In addition, this ToF surpasses the operating parameters of conventional ToF cameras up to 10m. Also, since the camera can top out at 120 FPS, you can get coherent images with this ToF sensor.
Additionally, you can change the IR filter in the 850nm and 940nm range. The 850nm filter has high sensitivity, giving you a better view of your image. At the same time, the 940nm filter will help you reduce glow interference, giving you the best depth image performance.
TFmini Plus - ToF Lidar Rangefinder
Source: Wikimedia Commons
This is another example that is well suited for single point short range ToF measurements. The TFmini plus LIDAR distance sensor can generate near infrared rays to measure the difference between emitted and reflected glare and obtain the ToF distance.
However, the lidar principle makes it difficult for such sensors to make precise measurements between objects such as glass or water. But its sensor is sensitive enough to measure the distance between a moving object and the TFmini in real time.
Also, you can get distance data on your PC by simply plugging in the TFmini via USB. Additionally, developers can take advantage of TFmini's UART and I2C interfaces.
Slamtec Mapper ToF Laser Scanner
Source: Wikimedia Commons
A ToF laser scanner is required; then this example is perfect for you. The scanner offers two different frames with different detection ranges:
40m
20m
The M1M1 is powerful enough to paint scenes for home or commercial use and well-lit locations.
You also get real-time location, state-of-the-art mapping and navigation with laser scanning. Also, you can use this device to map exterior and interior scenes.
This Slamtec scanner has excellent performance and is easy to operate without any hassle. You also don't need to rely on external tools. You just connect it to your PC or phone and you're all set.
Is the time-of-flight sensor PCB circuit board accurate?
The accuracy of any ToF sensor depends on the distance between the object and the sensor. Also, you estimate the accuracy of the ToF sensor to be 1% of the distance value. So if your object is 8 meters away, the ToF sensor can get an accuracy of about 8 centimeters.
Is LiDAR a ToF?
LIDAR is a form of ToF that uses a pulsed laser to generate point clouds that enable sensors to create 3D map images. Additionally, lidar systems use an LED that you can direct to emit infrared light.
-
No comment
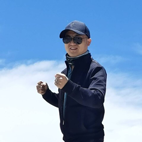