address:201, Factory 6, Longhui Industrial Park, Fuqiao 3rd District, Xinhe Community, Fuhai Street, Baoan District, Shenzhen china
Why PCBs are Green: The Science Behind the Color Choice
Printed Circuit Boards (PCBs) are the backbone of nearly all electronic devices. They act as the foundation upon which electronic components can be attached. But have you ever wondered why most PCBs are green in color? In this article, we will delve into the history and evolution of PCBs, the role of solder masks, and the reasons behind the color choice for PCBs. Let’s KFPCBA with explore the science behind the color choice for PCBs.
The History of PCB Manufacturing
The roots of PCB manufacturing can be traced back to the early 1900s with the creation of the first prototype PCB in 1903. However, it wasn’t until the 1950s and 60s that PCBs became a central component in electronic devices. As manufacturing techniques became more sophisticated, the use of PCBs grew exponentially.
The Role of Solder Mask in PCBs
A solder mask is a protective layer that is applied to the PCB’s surface. The layer provides protection against moisture, dust, and other contaminants. Without a solder mask, the electronic components on the PCB could corrode or short circuit. Solder masks also help to prevent solder bridges between the components.
Why Green?
So why is green the de facto color for PCBs? The answer lies in the chemical makeup of the solder mask that is used. The green color is the result of using a particular type of epoxy resin. During the manufacturing process, a liquid resin is applied to the PCB surface as a thin film. The resin is sensitive to ultraviolet light, which allows for fine-tuned details to be added to the solder mask. The solder mask is then cured using heat or ultraviolet light, which solidifies the liquid resin into a hard material.
The choice of green as the color for the solder mask was not a deliberate one but rather a product of circumstance. One major manufacturer of PCBs, the United States military, had a large supply of green epoxy resin that was initially designed for other purposes. The epoxy was then repurposed for PCB manufacturing due to its favorable qualities.
Apart from being a legacy choice, the color green has some advantages over other colors. It provides high contrast to the copper traces on the board, making it easier to visually inspect the connections. The green color also has a calming effect on the eyes, reducing the strain on workers who spend many hours inspecting PCBs.
However, there are also some disadvantages to using green solder masks. One downside is that it may not be aesthetically pleasing to some end-users who see the PCB, as it does not allow for much visual differentiation.
Other Colors of PCBs
While green is the most common color for PCBs, other colors can also be used. This might be important for manufacturers who want to differentiate their products or for design purposes. It is essential to note that the process of manufacturing a PCB with different colors involves using different types of epoxy resin.
The Future of PCB Manufacturing
PCBs have come a long way since the early 1900s, and there is still room for innovation. The industry is continually looking for ways to manufacture PCBs that are more efficient and have a smaller footprint. As manufacturing techniques become more sophisticated, newer materials may be developed that can replace the epoxy resin currently used for solder masks.
These advancements may also influence the color palette of PCBs. As manufacturing technology advances, it may become easier and more affordable to produce PCBs with different colors. However, green will likely remain the most common color for some time to come.
Conclusion
In conclusion, the choice of green as the color for solder masks used on PCBs was not a deliberate choice but rather a product of circumstance. The green color helps provide high contrast and is pleasing to the eye, making it easy for visual inspection. Other colors of PCBs are available and may be used for different applications or design purposes. As the manufacturing of PCBs evolves, we can expect innovative changes in the materials used and the color choices available.
-
No comment
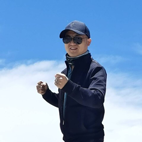