address:201, Factory 6, Longhui Industrial Park, Fuqiao 3rd District, Xinhe Community, Fuhai Street, Baoan District, Shenzhen china
Vol. 19, No. 3, Electronic Design Engineering (Lanzhou Institute Of Space Physics, Lanzhou, Gansu).
Vol. 19, No. 3, Electronic Design Engineering (Lanzhou Institute of Space Physics, Lanzhou, Gansu).
Volume 19
Issue 3 Electronic Design Engineering February 2011 V01.19 No. (‘. board design The expansion coefficient matching problem in Chenggang (Lanzhou Institute of Space Physics, Gansu Province) Abstract: Electronic product design is a systematic problem. The designer's attention is focused only on the design of the principle. Pay attention to the electrical performance indicators of the product. The problem of matching the expansion coefficient of components and raw materials is easy to ignore. This article starts with the matching of the expansion coefficient of components, substrates, solder, and other materials. This issue is analyzed. Solves a quality problem that may be caused by a mismatch in the swelling tie during product use. Keywords: circuit board design; Component: Expansion coefficient: mismatch Classification number: TN02 literature identification code: ang(00,China). : e . t,with . 。
al. This this .-al. inuostrich.words:;; (CTE); The reliability of electronic products is an eternal topic and pursuit. The achievable deformation of the product and the resulting stress cannot be changed. The dependence of any electronic product is influenced by a variety of elements. Among them, the machi reliability of welding is very Yingying's production core is the components that will meet the performance requirements. By the right approach one aspect. In order to pursue the miniaturization of products, more and more electronic products6^ use soldering (mounting) to printed circuit boards (PCBs) to form circuits with certain functions Surface mount technology (SMT ) to manufacture. Different from traditional through-hole cartridge 1=board assembly (PWA). In electronic assembly, meta-technology is generally completed by solder brazing. Surface mount technology uses the interconnection of surface-mount devices with no or short leads to the circuit board.
For the Tongxiao L Cartridge Technology (THT) welding with leaded components (SMD common MC), the problems related to the printed board and element components in the through-hole insertion art, the deformation stress caused by the expansion deformation of the printed board through the component lead, the "ugly" matching of the soldering material and other aspects become abrupt. The wire is buffered or absorbed by the deformation of the leads. The component body is first designed by the external product reliability. The design work includes the limited primary stress of the circuit obviously. The longer the component leads, the stress design transmitted to the component body, the selection of components, the design of printed boards, and the artistic design of products. The smaller the set. The stress generated by the solder during temperature changes is only on the solder joint itself as well as the welder... Welding problems caused by congenital deficiencies or errors. It is often difficult to bring an impact through the welding plate. Affects the reclicability of column solder joints. However, the use of surface mount technology processes has achieved all effective solutions, especially in batch production. Therefore. When assembling (SMT), although the installation density is increased. But the components themselves are designed as far as they are concerned. Not only should the electrical functional circuit be carefully designed, but there are no leads in the component for stress buffering and absorption. Stresses are transmitted directly to component selection, layout of circuit functions. The welding of circuit boards and components should be R-art, etc. Special attention. And combine the two. The design of nr relies on the functional circuit, which meets the CTE of the commonly used glass fiber reinforced substrate (FR--4) in: axis direction (perpendicular production T art requirements.
In order to improve the reliability of the product. straight to the plate plane) is different from the Z direction. In the direction of temperature, the expansion coefficient of components, substrates, solder, etc. will expand reliably with the temperature of the material. When the temperature is lower than the glass transition temperature, the material is in a glass state, and the sex has the effect of rain. Some studies131 indicate. At this time, the thermal expansion coefficient (CTE) of the packaged device is a1. When it is higher than the glass transition temperature, the main original flash for the failure under the foot is that the thermal expansion coefficient of each component material in the package is not in the colloidal state, and the thermal expansion coefficient (CTE) is a2. and is usually greater than dl (about nl The thermal stress problem caused by matching). In this paper, the expansion coefficient of the material is 3 times that of the crystal-producing welding). For example, when the temperature is lower than strong, the impact of CTE quality of glass fiber epoxy materials is explained and analyzed from the aspects of design and process measures. The direction of the z axis and the Y axis are also different, about the difference of l to 5ppm/oC. in the z direction is left and right; and when higher than Tg, the z direction port n accounts for 80ppm/°C left 1 The expansion coefficient of the material is right, see her table l. When the CTE of a large K-inch surface-mount device matches the substrate. The coefficient of thermal expansion of this material is one of the physical properties of the material. The change in temperature is very important for improving the life of the solder joint. Received:2010-08—25Manuscript Number: About author:Cheng Gang(1967a).Male. People from Tongchuan, Shaanxi. Master. Senior engineer. Chief Technologist of Lanzhou Institute of Space Physics.
Research interests: aerospace electronic product technology. ●-57- Wanfang Data "Electronic Design Engineering" 2011 No. 3 Table I Material characteristics of commonly used printed circuit boards.1of Maximum use temperature generation glass temperature, °C tensile strength, MPa material thermal conductivity, (w circuit board component quotation , m.K) X, Y hall, (pI)rIl, °C) CTEZ square (-j/(ppmPC) CTE is a surface mount PWA that affects the life of through-hole and microvia. Because its aspect ratio (substrate thickness to hole diameter) is usually better than just finished through-hole t. CJ Garding's printing plate has a large aspect ratio. In SMT reflow, device disassembly, resoldering, repair process, printed circuit board Electrical insulation/substrate such as manufacturing, ball wetting, hot air leveling and wave soldering, lower limit of material/system Typical value Upper limit Remarks During installation. If the CTE value in the Z direction is large, it will lead to excessive tension in the wall of the PI'H hole. Oka this. The selection of printed board substrate should first consider whether the thermal expansion coefficient (CTE) of the material and the thermal expansion coefficient of the installed components match. If it is not matched, compensatory measures should be taken.
At present, the printed circuit board substrates commonly used in the production of electronic products mainly include: organic substrates, ceramic substrates, and metal substrates. The most commonly used is epoxy glass cloth laminate (FR-4). Most of the traditional component soldering of electronic products will use tin-lead eutectic brazing. Quickly realize the conversion of solder from liquid to homomorphic to avoid disturbance when solder joints condense. Reduced soldering stress on components and good crystallization of solder. Lead-tin solder also has different CTE values. For components, it is generally composed of semiconductor silicon materials (chips), precision alloys (leads, etc.), ceramic materials (packaging materials), resin materials (packaging materials), etc. as a component. Manufacturers have generally made elaborate optimization designs through material selection. The overall CTE value of the component is optimized to avoid the mismatch of the coefficient of thermal expansion. Ceramic materials are commonly used as packaging materials in high-reliability electronic products to ensure the sealing performance and environmental resistance of components. The CTE characteristics of commonly used materials for components are shown in Table 2. Ceramic materials are a widely used material in the electronics industry. Including most resistor substrates, ceramic (monolith) capacitors, diode packages, etc. (glass also has some characteristics of ceramic materials). The property of hard and brittle is an innate characteristic of ceramic materials. The direction of the force applied on the ceramic substrate to generate the stretching stress and the component goes through the process of molten soldering, and the temperature change range can reach more than two hundred degrees, which compressive stress. When the force increases to reach compressive strength and tensile strength, fracture occurs, and the process directly affects the plated through-hole (frI'H blade V), pads, components and printing electricity In general. The compressive strength of ceramic materials is much greater than its tensile strength: in addition, it is determined by the quality and reliability of the road plate.
Other manufacturing processes with temperature changes include: There are more or less defects and microcracks in the material processing process, so the high-temperature baking of porcelain-based printed circuit boards, bonding wattle curing, and curing of composite coatings, The force required for plate fracture is much lower than the theoretical value. Temperature shock, environmental stress screening, etc. Therefore. The design considering the temperature change must take into account the influence of the expansion coefficient 2. The stress action between the materials caused by the temperature change. Scratch is the stress on the solder joint. Temperature changes are not only an assessment of the reliability of electronic components. Effect of Gang 3 stress on reliability The change of temperature will bring the problem of expansion deformation. Deformation creates stress. Throughout the life cycle of electronic products from production process to delivery to users, products undergo &l common stresses and undergo different environmental conditions. Especially temperature changes. Common stresses involved in the product manufacturing process generally include thermal stress, electrical stress, chemical stress and machine meal and ambient temperature changes. The most drastic processes of change should belong to the components and forces. Thermal stress includes a constant high or low temperature ambient temperature, and a cyclic ambient temperature -58- million square meters of data into steel The degree of expansion coefficient matching problem in circuit board design, the on-off cycle of the circuit leads to the cycle temperature change of the inner kettle. The circulation temperature will cause the iliac body to expand and lose its canth, mainly depending on 3 parameters: CTE small pt plus Aa. Thermogenic mechanical stress. The degree fluctuation range is the same as △r and the expansion shift. The overall expansion mismatch will cause a cycle of 3.2 temperature as an important ring force for the component to withstand stress.
and causes fatigue. Cyclic accumulation fatigue, strain damage will eventually lead to the loss of solder joints for component failure I machi occupy, temperature is the most eye-catching single stress effect factor, special Zhen is the corner joint of the solder joint. Plain. Especially in SMT [mouth l flow soldering process towel. Exposure to high temperatures can also lead to a 4.2 periodic expansion mismatch Some irreversible phenomena: the periodic temperature changes of components or substrates (△?'). With the outside 1) SMll integrated circuit package internal and external evils of delamination, cracks: chip table (daily) imposed on the component, base on the temperature change or l: imposed on the surface by mechanical damage, the formation of microcracks will become the chip will belong to the layer corrosion components, substrate L temperature changes. Since . The different work of the source component leads to the root cause of the failure. Passive component networks are also important for layering and fission. The temperature variation range of the component is significantly different from the temperature variation of the substrate. Sensitive to lines and corrosion; The difference in thermal expansion of components and substrates will lead to periodic expansion mismatch △a2) insulating electric alloy l will be greatly reduced, and the bearing of dielectric strength and mechanical strength (AT) will be greatly reduced. △71 The smaller the system, the better the reliability. Permanent loss of capacity; Surface mount (SMT) devices are soldered to the substrate by soldering. However, the coefficient of thermal expansion (CTE) of the device 3) of the capacitance, inductance, vibrating, resistance/capacitance network is melted at the junction of the solder joint, and the thermal expansion coefficient (CTE) is often different from the substrate. CTE mismatch between solder and substrate. or open circuit: Thus when the ambient temperature changes.
Mechanical shielding forces are generated at the solder joints. The mechanical stress on the component 4) including the coefficient of thermal expansion (CTE) of the material is a potential HR dependability problem. Each flexible layer on the surface of the substrate is limited to reduce the mismatch. Like what. SMT substrate fiberglass and hard ceramic components junction slow mismatch.fII. is not enough to offset the effect of large expansion mismatch. of Pili. Hard ceramic components include large multilayer capacitors, power resistors, mixed ceramic 4.3 local expansion mismatch Porcelain and inductor: Fatigue damage caused by CTE mismatch of solder and lead material l'HJ will cause 5) non-homomorphic electrolytic capacitors (such as aluminum, wet tantalum block) towel liquid boiling and steaming bureau qi expansion mismatch phenomenon. This reliability pl problem requires the use of boundary fault stress analysis. and the consequent loss of capacitance and the increase in equivalent series Hl: Method. Namely: 6) expansion of elastic materials. For example: j}j in sealed components (such as optocouplers, pulse local expansion mismatch four phenomena will cause interfacial stress: punch transformer, inductor and delay line) silicone resin or RTV, and the accompanying Lilly element under mL(d%",—ab)(ding'ah a ding. Canthus) (1) Breakage of leads, lead junctions. where: £ indicates the pin wetting length of the solder joint. That is, the length of the solder joint. In addition, at the interface of the solder joint 4 thermal expansion coefficient mismatch and the substrate being wetted. Except for the presence of the jade stress in r. There is also a greater coefficient of peeling linear thermal expansion, which refers to the linear separation of the size of the material when the storage temperature changes. Change. Components and substrates have a material that does not ask questions, that is, there is a thermal expansion system that does not have a gap It is obvious from Equation (1) that the length of the weld should be reduced to reduce the number: the effect of thermal expansion needs to pass the stress at the interface between the CTE of the material itself and the component material.
However, in most applications, the actual situation of local expansion loss can only be evaluated by comprehensive consideration. When the huh sex is expected. The damage caused by the match will exacerbate the loss caused by the overall thermal expansion mismatch The CTE must be analyzed if estimated. Injure. This rule is usually ignored without experiencing significant losses. CTE mismatch is when the coefficient of thermal expansion of two materials or parts in contact is not for components with long pins. Flash as pin n'to pass through its own material with . The difference is (Aa). In most cases, the c7I flying mismatch is mainly generated, and L adjusts the shape without plastic deformation of the device. Displacement or deformation caused by thermal expansion mismatch will not be directly between the substrate, but even more so. When the solder and bonding materials (e.g. ceramics, 42# junctions) are transferred to affect the solder joint and component body. Gold, Kovar alloy) will {l; The greater the expansion of the body and the undermatch H. and the greater the pin stiffness, the greater the stress. Leadless connection (table Local Expansion, Canine Mating. The latter affects the latter pair less. But not n'ignoring. Large face mount) form rigidity. Low stiffness pins provide higher reliability. Introduce the CTE mismatch into Yan Mu's nf dependence f'IJ problem. The pin of the hole is connected to the device, and the pin nT becomes a surface-mount pin nT to think that the ljI pin is very large, and the size of the component A connection affects the temperature change process of r, feverish expansion and contraction, and it is a hard limit case. In accelerated trials. or other special f] design special 1 two. The F spring of the component is the most placed movement of the original {r welded f. In a hot environment, it will generally be released! t-Large thermal expansion mismatch.
flj Therefore, in SMT with f, the larger the component, the greater the impact on ̈r dependency. Process H. Appropriately increase the solder height of the components. Through the solder of the cockroach!! 4.1 The overall expansion mismatch can slow down the magnitude of the internal stress. The overall expansion mismatch is caused by the influence of the electronic components connected by the solder joints on the above surface and 4.4 Temperature changes The thermal expansion of the printed circuit board is not "ljl". This thermal expansion chip of cerumen is | when red is short. H] Violent licking at two extreme temperatures, hot and cold. The hot and cold punch will be hot and cold due to the small M expansion coefficient of the material and the heat generated by the power components to catch the system towel. Hot Punch IL; is the most drastic temperature change. In this case, F-base rice is not in the river that is synthesized by the formation of a temperature gradient. From Theory J: swim when Aa a 2 is in thermal equilibrium. Flash this internal stress is sufficient to cause fracture. When }}j is enough to swell and undermatch. Due to the change of the temperature of the component and the printed circuit board, the f14△7', which will lead to the different CTE of the component, the material diversity determines that the thermal expansion of the same component is not matched in reality≤. The CTE mismatch at sMT state flow ppm/°C will be almost small. Soldering, wave soldering and }J: The soldering process will }lj present thermal shock. Extremely fast temperature-59-Wanfang Data, Electronic Design Engineering, No. 3, 2011 Degree changes (temperature rise of more than 30°C per minute) will produce large instantaneous thermal gradients, which will improve reliability to a degree.
The mouth "can directly cause distortion and warpage of the surface-mount component, and this warping process produces 1) coordination of the CTE of the material to reduce the overall thermal expansion mismatch. CTE takes the earned stress and shear stress. The tensile load is used to match the steady-state coefficient of thermal expansion and adjustment: material selection, or multilayer printed wiring board (MLB) or element mismatch play a dominant role. Oka this. Even the components with sufficient thermal expansion coefficient are combined with materials to achieve the optimal △C, Rotor. The optimal △C7rE will cause solder joints to fail under such thermal shock conditions. (depending on power consumption). Of course, due to the many elements contained in a component temperature and thermal cycling can lead to: system structure and use materials due to thermal expansion parts. The CTE matching of all components can achieve the optimal board component quotation, which requires the repeated stress of the optimal mismatch cattle to cause repeated bending and may cause fatigue. Immobilization of components that has the greatest impact on the town's reliability risk. Ceramic and organic components on organic and ceramic substrates are particularly sensitive (example 2) to increase connection compliance, such as increasing solder joint height, to coordinate overall thermal expansion mismatches. When the leads are formed and mounted to the printed board. Thermal stress relief should be taken such as: ceramic I 'cC components are also set on organic FR_4 substrates, or fin seals without devices "Sidingding: ceramic substrates"). Serious measures will cause cracks and measures in components due to overload. For the welding of leadless components, increasing the soldering compliance will increase the failure of the solder joint. Add solder joint height. Or replace it with a component that is soldered with leads.
For leaded large power consumption components. Even in the absence of components that match the CTE coefficient of the substrate, increasing soldering compliance is to use self-. It is better to mention the case. The power cycle change of the component itself is more affected than the change of ambient temperature, and the geometry of the high soldering compliance type is the component. of many. 3) Fill the gap between the component and the substrate. Other than that. Due to mechanical stress after welding (such as twisting and bending) or the Denso process 4) the stress at the interface is reduced by reducing the wetting length of the pins. Shock and vibration (e.g. TH'11 component stabs, PCB splitting, or testing) with 6 epilogues to the effect of mechanical stress. It can also cause damage to the component substrate and one end of the substrate interface and cause an open circuit. Therefore, it is necessary to identify the high-stress areas of the printed plate and improve the reliability of the product is the eternal standard of electronic products. Avoid placing large, susceptible devices in these areas. The PWA bending is minimized by improving the performance guarantee at the time of fixation, including subordinate components, circuit principle design, printed board design, T-art equipment support, and vibration damping. All aspects of metering, product manufacturing and environmental stress screening. Save the design link. It is also important to have thermal analysis in the design of red electronic packaging. In the condition of large temperature difference, the expansion coefficient matching problem of no device and printed wrench and solder problem is considered. Under. The following factors should be considered in the selection of materials: by reducing the difference in the expansion coefficient of the two. So as to reduce the internal stress caused by the change of glass in the temperature range of the polymer material due to the temperature 1) of the temperature to consider. To ensure that the electronics town works stably.
Melting temperature (Tg). The properties of the material change very significantly around Tg. References: 2) Due to very large thermal stress. Therefore, it is necessary to ensure that it has different thermal expansion systems [1] Zeng Shengzhi. Electronic welding design of SMT printed board[J]. Electronics & Packaging, 2005 Solid connections of materials, such as thermal stress, can cause fatigue failure of solder joints, adhesives (9): 13-14. Bonding failure. Ceramics and glass appear cracked, metal deformation, etc. When the temperature difference between different parts of an object is large. Even for short periods of time, thermal stress can occur. 【2J Chen Junan. Electronic components and manual soldering [MJ-Xi'an: China Water Conservancy and Hydropower 5 Reliability Design Edition.1998.In the design of printed boards, especially the design of printed boards for surface mounting, first [3] Zhang Yu. YANG Xuexia, ZHAO Zhendong, et al. The influence of solder joint shape on the reliability of solder joint The CTE gallbladder of the material should be considered first. When selecting the material for printing the wrench, the factory should solve the problem Pi 13/OL].China Science and Technology Papers Online.http://www.paper.edu.on. — The packaging form of the component and the material of the substrate and the sensing of the component soldering T. art b)of[4L Group(— The change range of temperature. Select a substrate with a matching coefficient of thermal expansion to reduce the thermal stress caused by the difference in the coefficient of thermal expansion of the material.
The temperature is the design process of surface mount printed circuit board assemblies () in 1996. USA,IPC. July is one of the environmental factors that must be taken into account. In the practical application of some products, the . [M]. New use of the environment to affect the fatigue life of the product is the most important Gangsu. This is in Product Development.1991:413-450. What is considered before the final design is finalized in the cycle. Therefore. The reliability design depends to a large extent on the thermal design of the component and the external thermal environment.·,【S1.1'he reasonable method of improving reliability to take the following methods. With the maximum limit of ion, 2008.Welcome to subscribe to the 201 "Electronic Design Engineering" (semi-monthly) Domestic postal code: 52-142 International issue code: M2996 Price: 6.∞ yuan/period: 144.00 yuan/year —60— Wanfang Data Coefficient Matching Problems in Board Design Author:Cheng Gang, Cheng Gang Author:Lanzhou Institute of Space Physics,Lanzhou,Gansu,Gansu,Title:Electronic Design Engineering English Title: Year, Volume (Issue):2011,19( 3) References (6 articles) 1.ESA-ESTEC, ECSS-Q-ST-70-38C. High- for -mount and mixed 2008 2.John Lau Joint 1991 3.IPC Task Group (7-31b)ofthe (7-30)of IPC,IPC-D-279 for Mount Board 1996 4.Zhang Yu; Yang Xuexia; Zhao Zhendong Influence of solder joint shape on solder joint reliability 5. Chen Junan Electronic Components and Manual Soldering 1998 6. Zeng Shengzhi Electronic welding design of SMT printed board 2005(09) Link to this article: /.aspx
-
No comment
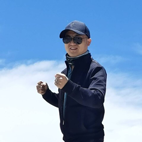