address:201, Factory 6, Longhui Industrial Park, Fuqiao 3rd District, Xinhe Community, Fuhai Street, Baoan District, Shenzhen china
What do SMD and SMT mean in PCBA processing?
SMT and SMD. These two small acronyms are lumped together in the field of electronics manufacturing services. , they differ by only one letter, but in practice SMT and SMD are much more different.
SMT stands for Surface Mount Technology, the entire technique of mounting and soldering electronic components such as resistors, capacitors, transistors, integrated circuits onto a printed circuit board or PCB. The components used are also called surface mount devices (SMD, surface-mount devices). It should be noted that SMT does not need to reserve corresponding through holes for component pins, and SMD is much smaller than through hole insertion technology.
What is Form SMD?
Surface Mount Devices (SMDs) are small components attached to circuit boards in electronics manufacturing. They are designed to be smaller than previous components in response to the market demand for smaller, faster and cheaper electronics. Through-hole technology cannot keep up with increasingly compact and complex technologies throughout the late 20th and 21st centuries.
The previous components were not only larger, but required a different and slower application process. In older component versions, the wires would go through the board, whereas SMDs used pins that were soldered to pads on the board. This means more efficient use of board space as no holes are required and both sides of the board become available space.
SMDs were created to work with efficient and precise Surface Mount Technology (SMT).
What is Surface Mount Technology or SMT?
Surface Mount Technology or SMT is the process of mounting and soldering surface mount components to a board.
During this process, the amount of solder paste applied is calculated so that the stencil is perfectly aligned on the surface of the board. Then, a pick-and-place machine uses the template to mount the components to the board. Next, the board goes through an infrared oven, which melts the solder paste and forms solder joints. This very precise process is done with an automated optical inspection machine that checks alignment and quality.
Features of SMT:
Components have no leads or only short leads;
The component body and the solder joint are on the same side of the PCB;
Features of SMD:
miniaturization;
No leads (flat or short leads);
Suitable for surface assembly on PCB;
Where SMT and SMD come together
In the early days of SMD, smaller, more complex components had to be placed and soldered manually. Machines can do some work, but only in size and type. Today, using SMT to make circuit boards is somewhat similar, but faster and more precise.
At that time, small pieces of silver or lead were placed on the board to connect the components. These elements are still used, but in solder paste it is a mixture of flux and a small amount of solder. An SMT machine can connect thousands of SMDs per hour, while a manual might have only a few hundred. As a result, almost every through-hole process now has an SMT equivalent.
Advantages of SMT: reduce PCB area; reduce weight, easy to automate installation; reduce parasitic capacitance and parasitic inductance; improve product quality and reliability;
SMT brings a new generation of electronic assembly technology, which is widely used in fields such as aviation, communications, automobiles, medical electronics, and household appliances.
KFPCBA provides a complete turnkey service including parts procurement and assembly. Whether you're prototyping or scaling up, KFPCBA is your one-stop destination for smooth, hassle-free PCB assembly.
-
No comment
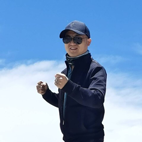