address:201, Factory 6, Longhui Industrial Park, Fuqiao 3rd District, Xinhe Community, Fuhai Street, Baoan District, Shenzhen china
Top 11 Must-Know PCB Assembly (PCBA) Equipment and Tools
Have you ever considered the costs and equipment required for manufacturing PCB products? What about the number of people needed to produce an order of 10,000 printed circuit boards (PCBs)?
Your PCB assembly shop will not become the best in town without proper equipment magically.
It is good to be aware of some of these factors as they can help you decide on outsourcing your PCB assembly project.
In this talk, we'll review the 11 must-know PCB assembly equipment that you need to make your shop the best. Would you like to know some commercial secrets? You're in the right place!
Top 11 Must-Know PCB Assembly (PCBA) Tools
Solder Paste Printing Machine
The primary function of this machine is to print the solder paste on the PCB. It can be used for both reflow soldering and wave soldering. The main parts of this machine are an extruder, a solder paste pump, and a dispensing head.
The solder paste extruded from the extruder is pumped by the pump and then dispensed onto the printed circuit board by the dispensing head.
The solder paste must be delivered accurately to ensure no dry spots or excess solder on the board. This machine can also be used for printing other materials such as epoxy resin, adhesive and conductive ink.
Soldering Iron (Soldering Station)
The soldering iron has two main parts: a heater element and a tip (also known as a tip temperature controller). The heater element heats up until it reaches its melting point; meanwhile, the tip temperature controller regulates how hot it gets by adjusting the power input to its heating element.
When soldering, you need to regulate both these temperatures so that your soldering iron will work properly and produce good quality joints without damaging components or boards during use.
Solder Paste Inspection (SPI) Machine
The SPI machine is used to inspect solder paste for defects such as missing or excess tin, non-uniformity of the solder paste, and color variation between different locations on the PCB.
This machine can also detect the presence of particulates in the solder paste and possible particles on the die pad area. The SPI machine can be used with an optical microscope or a scanning electron microscope (SEM).
Solder Paste Printing (SPP) Machine
The SPP machine prints solder paste onto the PCB using an inkjet printer head similar to the one used in an office printer or even a desktop copier/printer. This device prints small amounts of solder paste onto a PCB substrate before placing components onto it during assembly operations.
This process allows manufacturers to control their manufacturing processes and eliminate any potential mistakes caused by human error when manually placing components during assembly operations.
Glue Dispensing Machine
The glue dispensing machine automatically applies a thin layer of glue to the PCB board surface. The glue dispensing machine is usually installed in the production line and operates automatically.
The first step is to load the raw material into the machine, which can be done manually or automatically. Then you need to set the parameters according to different types of boards, such as single-sided boards, double-sided boards, and multilayer boards.
After that, it will start to work automatically once it receives electricity from 220V. The glue will be sprayed onto the PCB board surface at a certain speed through a nozzle with a certain pressure and thickness according to your requirements.
Pick-And-Place Machine
The pick-and-place machine is a device that automatically places components onto the circuit board (PCB) in a controlled, repeatable manner. The PCB must be appropriately placed to work as expected for the result.
The goal of the pick-and-place machine is to apply components to PCBs as fast and accurately as possible without damaging the components or the PCB.
The pick-and-place machine can place any component onto the PCB. The composition of the pick-and-place device depends on the operations required for each element.
For example, a pick-and-place machine for SMD components will have an X/Y table with high-precision optical sensors to position the parts correctly.
For more significant parts (passives and ICs), you'll need a vacuum nozzle system that can handle these components. In addition, a high-precision vacuum system is required to hold down each part.
Other essential features are thermocouple or infrared temperature sensors to detect hot spots generated by high-power devices such as LEDs and FETs. This feature ensures that all components are operating at appropriate temperatures and prevents damage to them due to overheating.
Reflow Soldering Machine
The rework soldering machine is a component used in the assembly process, and it plays an essential role in the quality of the finished product.
Many people who are just starting as technicians are often neglected, but it should be understood that without this machine, the entire production process would be stopped dead in its tracks.
The purpose of the rework soldering machine is to make electrical connections between various components and other parts soldered together or coated with solder paste. These machines can also be used for rework processes; therefore, they are also known as rework stations.
While there are several different types of these machines available today, most of them work by heating parts and applying pressure at very high temperatures.
Technicians need to know that when working with rework stations, certain precautions and safety measures must be observed.
Wave Soldering Machine (For Through-Hole Components)
A wave soldering machine is the most popular way to solder through-hole components onto a PCB. It's one of the simplest, cheapest, and most versatile methods. It allows for high production volume and works well with many different materials and technologies.
A wave soldering machine uses a continuous wave of molten solder to flow over the components as they pass through a temperature-controlled oven.
Wave soldering machines are designed to be used in mass manufacturing environments with high throughput. They must be robust enough to handle large boards with many components being soldered simultaneously.
This means that almost all wave soldering machines are designed for boards between 1in2 and 2in2, with a maximum height of 0.185in or 4 mm above the board's surface when it passes through the oven.
A wave soldering machine can be used to solder through-hole or surface mount devices by adjusting its temperature profile. The giant machines use two separate temperature zones; one for soldering the lead of the through-hole component and another for soldering its body.
Automatic Optical Inspection (AOI) Machine
This system is used to inspect components such as BGA's, QFNs, and DIPs and through holes for defects such as missing component pins or pads, misalignment of features, and possible contaminants on component pads.
This system can also detect short circuits between adjacent pins during testing after assembly has been completed.
The output of this system is typically sent to an OPC server where it can be analyzed by technicians who will determine if the board should be scrapped or reworked if possible before being shipped out to customers.
In-Circuit Test (ICT) Fixture
The ICT fixture is used to test PCBs after they've been assembled. This fixture connects the PCB to a power supply like the one found in most consumer electronics products—your phone charger or laptop computer, for example—and has some indicator light to indicate when the board is powered up.
The light will blink when the board is powered on, so you can test whether all of your components are working correctly and whether any traces on your board are shorting out.
It's imperative to use an ICT fixture when testing boards with surface-mounted components because it reduces the number of external connections required.
Functional Validation Test (FVT) Fixture
If you're looking to test the functionality of your product before sending it through your automated assembly line, a functional validation test fixture is the way to go.
The FVT fixture is a portion of hardware that allows you to connect components or subassemblies and then run tests on those components or subassemblies and analyze the results.
These tests can be as simple as verifying that each component is making contact with other members within the system or as complex as testing all of the elements within a plan to ensure that they function independently, collectively, and together in a system.
In some cases, FVT fixtures are used after automated assembly systems have been implemented to ensure that all systems are functioning correctly and are not defective before they leave the factory.
Bottom Line
With the above list of 11 PCBA equipment, you will be able to create a successful PCB assembly line. If you also know how to design a simple circuit diagram and layout, you can start your own business online or offline.
Just make sure that your friends and family are not starving for money. You might be surprised about what little money you can get from doing PCB assembling in bulk production.
To get a reasonable price for your PCB assembly, study the market and get quotes from vendors before placing an order.
Finally, for any inquiries, questions, or comments, feel free to contact us. We’ll get back to you as soon as we can.
-
No comment
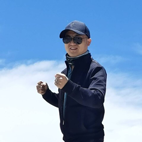